പ്ലാസ്റ്റിക് ഭാഗങ്ങൾ എങ്ങനെ രൂപകൽപ്പന ചെയ്യാം
ഹൃസ്വ വിവരണം:
ടു പ്ലാസ്റ്റിക് ഭാഗങ്ങൾ രൂപകൽപ്പന ചെയ്യുകഉൽപ്പന്നത്തിൽ ഭാഗങ്ങൾ വഹിക്കുന്ന പങ്ക്, പ്ലാസ്റ്റിക്ക് രൂപപ്പെടുത്തൽ പ്രക്രിയയുടെ ചട്ടം എന്നിവ അടിസ്ഥാനമാക്കി ഭാഗങ്ങളുടെ ആകൃതി, വലുപ്പം, കൃത്യത എന്നിവ നിർവ്വചിക്കുക എന്നതാണ്. അന്തിമ output ട്ട്പുട്ട് പൂപ്പൽ, പ്ലാസ്റ്റിക് ഭാഗം എന്നിവയുടെ നിർമ്മാണത്തിനുള്ള ഡ്രോയിംഗുകളാണ്.
ഉൽപ്പന്ന നിർമ്മാണം രൂപകൽപ്പനയിൽ ആരംഭിക്കുന്നു. പ്ലാസ്റ്റിക് ഭാഗങ്ങളുടെ രൂപകൽപ്പന ഉൽപന്നത്തിന്റെ ആന്തരിക ഘടന, വില, പ്രവർത്തനം എന്നിവയുടെ തിരിച്ചറിവിനെ നേരിട്ട് നിർണ്ണയിക്കുന്നു, കൂടാതെ പൂപ്പൽ ഉൽപാദനം, വില, സൈക്കിൾ എന്നിവയുടെ അടുത്ത ഘട്ടവും അതുപോലെ തന്നെ ഇഞ്ചക്ഷൻ മോൾഡിംഗും പോസ്റ്റ്-പ്രോസസ്സിംഗ് പ്രക്രിയയും ചെലവും നിർണ്ണയിക്കുന്നു.
ആധുനിക സമൂഹത്തിലെ വിവിധ ഉൽപ്പന്നങ്ങളിലും സ facilities കര്യങ്ങളിലും ജനങ്ങളുടെ ജീവിതത്തിലും പ്ലാസ്റ്റിക് ഭാഗങ്ങൾ വ്യാപകമായി ഉപയോഗിക്കുന്നു. പ്ലാസ്റ്റിക് ഭാഗങ്ങൾക്ക് വ്യത്യസ്ത ആകൃതികളും പ്രവർത്തനങ്ങളും ആവശ്യമാണ്. അവർ പ്ലാസ്റ്റിക് വസ്തുക്കൾ ഉപയോഗിക്കുന്നു, അവയുടെ സ്വഭാവവും വൈവിധ്യപൂർണ്ണമാണ്. അതേസമയം, വ്യവസായത്തിൽ പ്ലാസ്റ്റിക് ഭാഗങ്ങൾ നിർമ്മിക്കാൻ നിരവധി മാർഗങ്ങളുണ്ട്. അതിനാൽ പ്ലാസ്റ്റിക് ഭാഗങ്ങൾ രൂപകൽപ്പന ചെയ്യുന്നത് ലളിതമായ ജോലിയല്ല.
വ്യത്യസ്ത ഭാഗ രൂപകൽപ്പനയും മെറ്റീരിയലും വ്യത്യസ്ത പ്രോസസ്സിംഗ് നിർമ്മിക്കുന്നു. പ്ലാസ്റ്റിക് രൂപപ്പെടുത്തുന്നതിനുള്ള പ്രോസസ്സിംഗ് പ്രധാനമായും ചുവടെ ഉൾക്കൊള്ളുന്നു:
1.ഇഞ്ചക്ഷൻ മോൾഡിംഗ്
2. പൊട്ടുന്ന മോൾഡിംഗ്
3.കമ്പ്രഷൻ മോൾഡിംഗ്
4.റോട്ടേഷണൽ മോൾഡിംഗ്
5.തർമോഫോർമിംഗ്
6.extrusion
7. ഫാബ്രിക്കേഷൻ
8.ഫോമിംഗ്
വൻതോതിൽ ഉൽപാദിപ്പിക്കാൻ നിരവധി മാർഗങ്ങളുണ്ട്. ഇഞ്ചക്ഷൻ മോൾഡിംഗ് ജനപ്രിയ ഉൽപാദന രീതിയാണ്, കാരണം 50% ~ 60% പ്ലാസ്റ്റിക് ഭാഗങ്ങൾ നിർമ്മിക്കുന്നത് ബൈബ് ഇഞ്ചക്ഷൻ മോൾഡിംഗ് ആണ്, ഇത് ഉയർന്ന വേഗതയുള്ള ഉൽപാദന ശേഷിയാണ്.
ഞങ്ങൾ രൂപകൽപ്പന ചെയ്ത ചില പ്ലാസ്റ്റിക് ഭാഗങ്ങൾക്കായി കേസ് കാണിക്കുക:
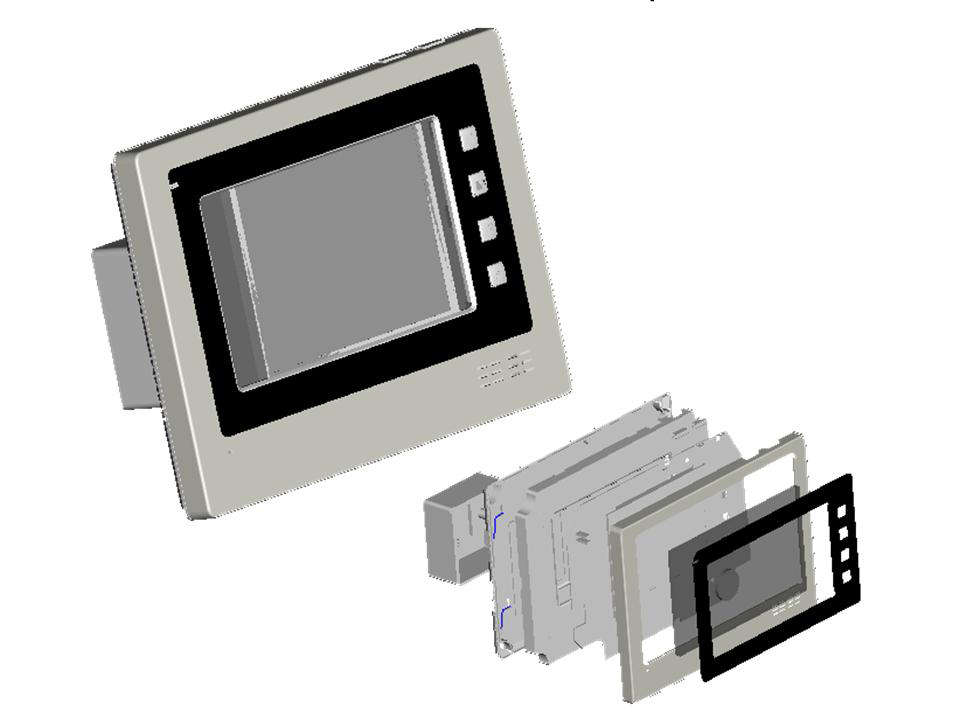
വിഷൻ ഫോണിന്റെ പ്ലാസ്റ്റിക് വലയം
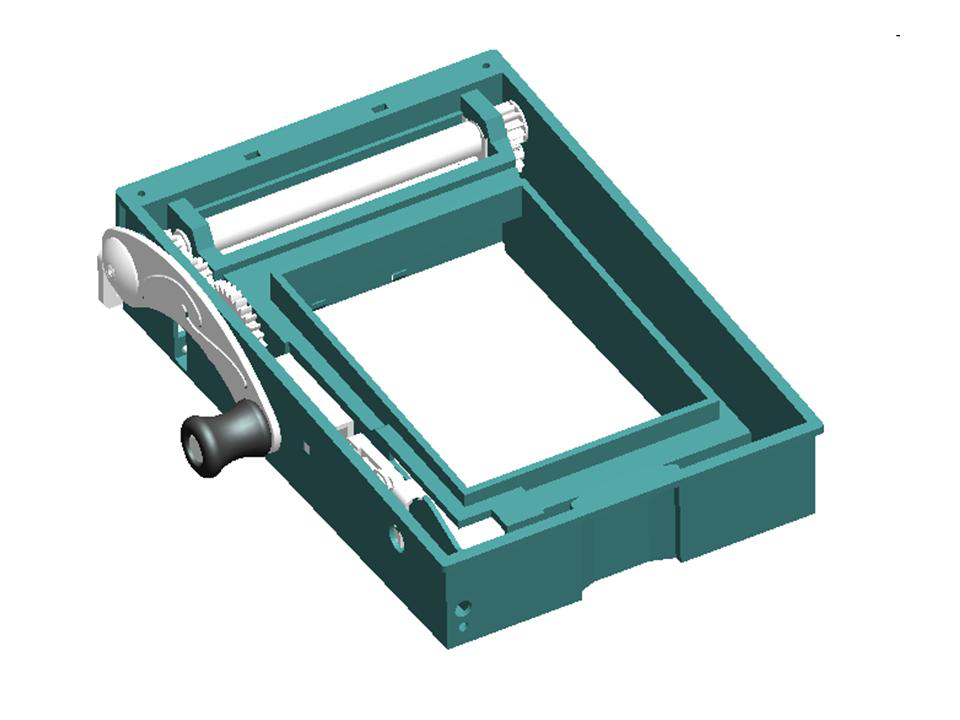
മെക്കാനിസത്തിന്റെ പ്ലാസ്റ്റിക് ഭാഗങ്ങൾ
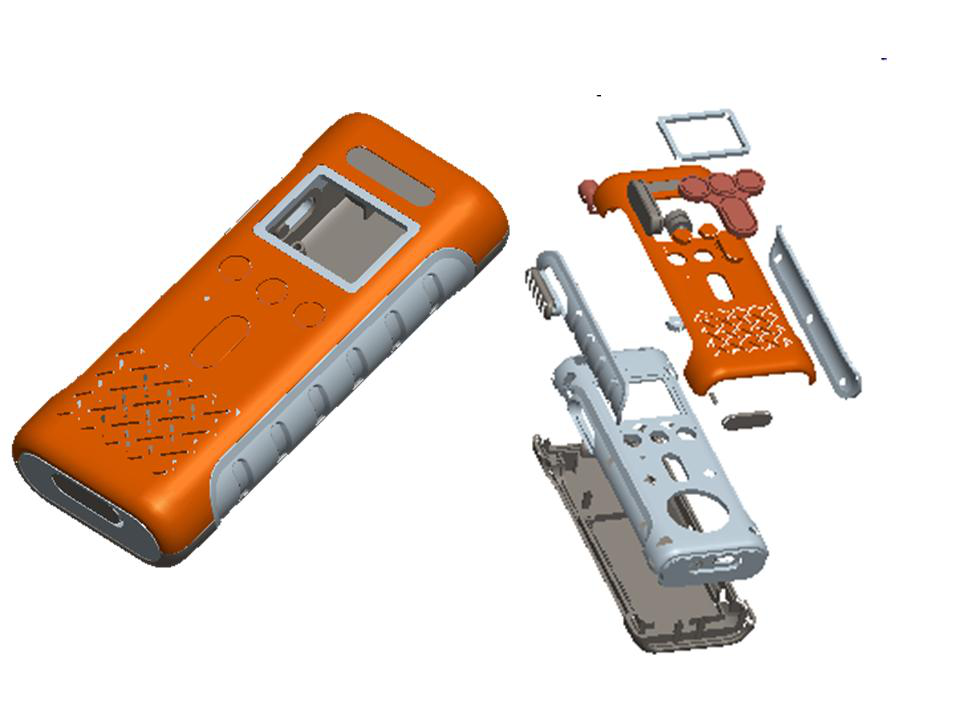
ഇലക്ട്രോണിക് പ്ലാസ്റ്റിക് കേസുകൾ
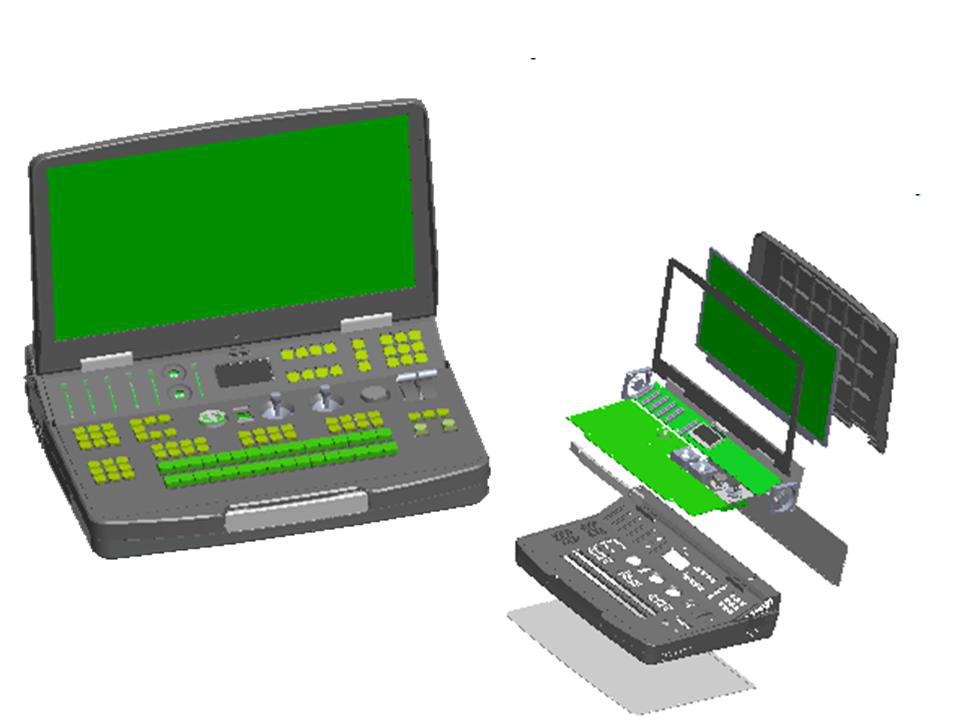
ഉപകരണത്തിനുള്ള പ്ലാസ്റ്റിക് ഭവനം
മൂന്ന് വശങ്ങളിൽ പ്ലാസ്റ്റിക് ഭാഗങ്ങൾ എങ്ങനെ രൂപകൽപ്പന ചെയ്യാമെന്ന് ഞങ്ങൾ ചുവടെ പങ്കിടുന്നു
* നിങ്ങൾ അറിഞ്ഞിരിക്കേണ്ട പ്ലാസ്റ്റിക് ഭാഗങ്ങൾ രൂപകൽപ്പന ചെയ്യുന്നതിനുള്ള 10 ടിപ്പുകൾ
1. ഉൽപ്പന്നത്തിന്റെ രൂപകൽപ്പനയും വലുപ്പവും നിർണ്ണയിക്കുക.
മുഴുവൻ ഡിസൈൻ പ്രക്രിയയുടെയും ആദ്യ ഘട്ടമാണിത്. വിപണി ഗവേഷണത്തിനും ഉപഭോക്തൃ ആവശ്യകതകൾക്കും അനുസരിച്ച്, ഉൽപ്പന്നങ്ങളുടെ രൂപവും പ്രവർത്തനവും നിർണ്ണയിക്കുക, ഉൽപ്പന്ന വികസന ചുമതലകൾ രൂപപ്പെടുത്തുക.
വികസന ചുമതല അനുസരിച്ച്, വികസന ടീം ഉൽപ്പന്നത്തിന്റെ സാങ്കേതികവും സാങ്കേതികവുമായ സാധ്യതാ വിശകലനം നടത്തുന്നു, കൂടാതെ ഉൽപ്പന്നത്തിന്റെ 3D രൂപ മാതൃക നിർമ്മിക്കുകയും ചെയ്യുന്നു. തുടർന്ന്, ഫംഗ്ഷൻ തിരിച്ചറിവും ഉൽപ്പന്ന അസംബ്ലിയും അനുസരിച്ച്, സാധ്യമായ ഭാഗങ്ങൾ ആസൂത്രണം ചെയ്യുന്നു.
2. ഉൽപ്പന്ന ഡ്രോയിംഗുകളിൽ നിന്ന് വ്യക്തിഗത ഭാഗങ്ങൾ വേർതിരിക്കുക, പ്ലാസ്റ്റിക് ഭാഗങ്ങൾക്കായി പ്ലാസ്റ്റിക് റെസിൻ തരം തിരഞ്ഞെടുക്കുക
മുമ്പത്തെ ഘട്ടത്തിൽ ലഭിച്ച 3 ഡി മോഡലിൽ നിന്ന് ഭാഗങ്ങൾ വേർതിരിച്ച് അവയെ വ്യക്തിഗതമായി രൂപകൽപ്പന ചെയ്യുക എന്നതാണ് ഈ ഘട്ടം. ഭാഗങ്ങളുടെ പ്രവർത്തനപരമായ ആവശ്യങ്ങൾക്കനുസരിച്ച്, അനുയോജ്യമായ പ്ലാസ്റ്റിക് അസംസ്കൃത വസ്തുക്കളോ ഹാർഡ്വെയർ വസ്തുക്കളോ തിരഞ്ഞെടുക്കുക. ഉദാഹരണത്തിന്, എബിഎസ് സാധാരണയായി
ഷെൽ, എബിഎസ് / ബിസി അല്ലെങ്കിൽ പിസിക്ക് ചില മെക്കാനിക്കൽ ഗുണങ്ങൾ, ലാമ്പ്ഷെയ്ഡ്, ലാമ്പ് പോസ്റ്റ് പിഎംഎംഎ അല്ലെങ്കിൽ പിസി, സുതാര്യമായ ഭാഗങ്ങൾ, ഗിയർ അല്ലെങ്കിൽ വസ്ത്രം ഭാഗങ്ങൾ POM അല്ലെങ്കിൽ നൈലോൺ എന്നിവ ആവശ്യമാണ്.
ഭാഗങ്ങളുടെ മെറ്റീരിയൽ തിരഞ്ഞെടുത്ത ശേഷം, വിശദമായ ഡിസൈൻ ആരംഭിക്കാൻ കഴിയും.
3. ഡ്രാഫ്റ്റ് ആംഗിളുകൾ നിർവചിക്കുക
ഡ്രാഫ്റ്റ് ആംഗിളുകൾ അച്ചിൽ നിന്ന് പ്ലാസ്റ്റിക് നീക്കംചെയ്യാൻ അനുവദിക്കുന്നു. ഡ്രാഫ്റ്റ് ആംഗിളുകൾ ഇല്ലാതെ, നീക്കംചെയ്യുമ്പോൾ ഉണ്ടാകുന്ന സംഘർഷം കാരണം ഈ ഭാഗം കാര്യമായ പ്രതിരോധം നൽകും. ഡ്രാഫ്റ്റ് ആംഗിളുകൾ ഭാഗത്തിന്റെ അകത്തും പുറത്തും ഉണ്ടായിരിക്കണം. ആഴമേറിയ ഭാഗം, ഡ്രാഫ്റ്റ് ആംഗിൾ വലുതാണ്. ഒരു ഇഞ്ചിന് 1 ഡിഗ്രി ഡ്രാഫ്റ്റ് ആംഗിൾ എന്നതാണ് ലളിതമായ പെരുമാറ്റം. ആവശ്യത്തിന് ഡ്രാഫ്റ്റ് ആംഗിൾ ഇല്ലാത്തതിനാൽ ഭാഗത്തിന്റെ വശങ്ങളിൽ സ്ക്രാപ്പുകൾ കൂടാതെ / അല്ലെങ്കിൽ വലിയ ഇജക്ടർ പിൻ അടയാളങ്ങൾ ഉണ്ടാകാം (ഇതിൽ പിന്നീട് കൂടുതൽ).
പുറത്തെ ഉപരിതലത്തിന്റെ ഡ്രാഫ്റ്റ് കോണുകൾ: ആഴമേറിയ ഭാഗം, ഡ്രാഫ്റ്റ് ആംഗിൾ വലുതാണ്. ഒരു ഇഞ്ചിന് 1 ഡിഗ്രി ഡ്രാഫ്റ്റ് ആംഗിൾ എന്നതാണ് ലളിതമായ പെരുമാറ്റം. ആവശ്യത്തിന് ഡ്രാഫ്റ്റ് ആംഗിൾ ഇല്ലാത്തതിനാൽ ഭാഗത്തിന്റെ വശങ്ങളിൽ സ്ക്രാപ്പുകൾ കൂടാതെ / അല്ലെങ്കിൽ വലിയ ഇജക്ടർ പിൻ അടയാളങ്ങൾ ഉണ്ടാകാം (ഇതിൽ പിന്നീട് കൂടുതൽ).
സാധാരണയായി, ഭംഗിയുള്ള ഉപരിതലമുണ്ടാകുന്നതിന്, ഭാഗങ്ങളുടെ ഉപരിതലത്തിൽ ടെക്സ്ചർ നിർമ്മിക്കുന്നു. ടെക്സ്ചർ ഉള്ള മതിൽ പരുക്കനാണ്, സംഘർഷം വലുതാണ്, അത് അറയിൽ നിന്ന് നീക്കംചെയ്യുന്നത് എളുപ്പമല്ല, അതിനാൽ ഇതിന് ഒരു വലിയ ഡ്രോയിംഗ് ആംഗിൾ ആവശ്യമാണ്. വലിയ ഡ്രാഫ്റ്റിംഗ് ആംഗിൾ ആവശ്യമാണ് എന്നതാണ് നാടൻ ഘടന.
മതിൽ കനം / ഏകീകൃത കനം നിർവചിക്കുക
ഇനിപ്പറയുന്ന കാരണങ്ങളാൽ ഇഞ്ചക്ഷൻ മോൾഡിംഗിൽ സോളിഡ് ഷേപ്പ് മോൾഡിംഗ് ആവശ്യമില്ല:
1) .കൂളിംഗ് സമയം മതിൽ കട്ടിയുള്ള ചതുരത്തിന് ആനുപാതികമാണ്. ഖരരൂപത്തിലുള്ള നീണ്ട തണുപ്പിക്കൽ സമയം വൻതോതിലുള്ള ഉൽപാദനത്തിന്റെ സമ്പദ്വ്യവസ്ഥയെ പരാജയപ്പെടുത്തും. (താപത്തിന്റെ മോശം കണ്ടക്ടർ)
2) .തിക്കർ വിഭാഗം നേർത്ത വിഭാഗത്തേക്കാൾ ചുരുങ്ങുന്നു, അതുവഴി വാർപേജ് അല്ലെങ്കിൽ സിങ്ക് മാർക്ക് മുതലായ ഡിഫറൻഷ്യൽ ചുരുങ്ങൽ അവതരിപ്പിക്കുന്നു (പ്ലാസ്റ്റിക്കുകളുടെയും പിവിടി സ്വഭാവങ്ങളുടെയും സങ്കോച സവിശേഷതകൾ)
അതിനാൽ പ്ലാസ്റ്റിക് ഭാഗം രൂപകൽപ്പന ചെയ്യുന്നതിന് ഞങ്ങൾക്ക് അടിസ്ഥാന നിയമമുണ്ട്; കഴിയുന്നിടത്തോളം മതിൽ കനം ഭാഗം ഏകതാനമോ സ്ഥിരമോ ആയിരിക്കണം. ഈ മതിൽ കനം നാമമാത്ര മതിൽ കനം എന്ന് വിളിക്കുന്നു.
ഭാഗത്ത് ഏതെങ്കിലും സോളിഡ് സെക്ഷൻ ഉണ്ടെങ്കിൽ, കോർ അവതരിപ്പിച്ച് അത് പൊള്ളയാക്കണം. ഇത് കാമ്പിനു ചുറ്റുമുള്ള ഏകീകൃത മതിൽ കനം ഉറപ്പാക്കണം.
3) .മതിൽ കനം നിർണ്ണയിക്കുന്നതിനുള്ള പരിഗണനകൾ എന്തൊക്കെയാണ്?
ഇത് കട്ടിയുള്ളതും ജോലിയ്ക്ക് വേണ്ടത്ര കടുപ്പമുള്ളതുമായിരിക്കണം. മതിൽ കനം 0.5 മുതൽ 5 മിമി വരെയാകാം.
ഇത് വേഗത്തിൽ തണുക്കാൻ പര്യാപ്തമായ നേർത്തതായിരിക്കണം, അതിന്റെ ഫലമായി താഴ്ന്ന ഭാഗത്തിന്റെ ഭാരം, ഉയർന്ന ഉൽപാദനക്ഷമത.
മതിൽ കട്ടിയിലെ ഏതെങ്കിലും വ്യതിയാനം കഴിയുന്നത്ര കുറഞ്ഞത് സൂക്ഷിക്കണം.
വ്യത്യസ്ത മതിൽ കനം ഉള്ള ഒരു പ്ലാസ്റ്റിക് ഭാഗം വ്യത്യസ്ത തണുപ്പിക്കൽ നിരക്കുകളും വ്യത്യസ്ത സങ്കോചങ്ങളും അനുഭവിക്കും. അത്തരം സന്ദർഭങ്ങളിൽ അടുത്ത സഹിഷ്ണുത കൈവരിക്കുന്നത് വളരെ പ്രയാസകരവും പല തവണ അസാധ്യവുമാണ്. മതിൽ കനം വ്യതിയാനം അനിവാര്യമായിടത്ത്, ഇവ രണ്ടും തമ്മിലുള്ള മാറ്റം ക്രമേണ ആയിരിക്കണം.
5. ഭാഗങ്ങൾ തമ്മിലുള്ള കണക്ഷൻ ഡിസൈൻ
സാധാരണയായി നമ്മൾ രണ്ട് ഷെല്ലുകൾ തമ്മിൽ ബന്ധിപ്പിക്കേണ്ടതുണ്ട്. ആന്തരിക ഘടകങ്ങൾ (പിസിബി അസംബ്ലി അല്ലെങ്കിൽ മെക്കാനിസം) സ്ഥാപിക്കുന്നതിന് അവയ്ക്കിടയിൽ ഒരു അടഞ്ഞ മുറി രൂപീകരിക്കുക.
സാധാരണ തരത്തിലുള്ള കണക്ഷൻ:
1). സ്നാപ്പ് ഹുക്കുകൾ:
ചെറുതും ഇടത്തരവുമായ ഉൽപ്പന്നങ്ങളിൽ സ്നാപ്പ് ഹുക്സ് കണക്ഷൻ സാധാരണയായി ഉപയോഗിക്കുന്നു. സ്നാപ്പ് ഹുക്കുകൾ സാധാരണയായി ഭാഗങ്ങളുടെ അറ്റത്ത് സജ്ജീകരിച്ചിരിക്കുന്നു, മാത്രമല്ല ഉൽപ്പന്ന വലുപ്പം ചെറുതാക്കാം എന്നതാണ് ഇതിന്റെ സവിശേഷത. ഒത്തുചേരുമ്പോൾ, സ്ക്രൂഡ്രൈവർ, അൾട്രാസോണിക് വെൽഡിംഗ് ഡൈ, തുടങ്ങിയ ഉപകരണങ്ങൾ ഉപയോഗിക്കാതെ ഇത് നേരിട്ട് അടയ്ക്കുന്നു. സ്നാപ്പ് ഹുക്കുകൾ പൂപ്പൽ കൂടുതൽ സങ്കീർണ്ണമായേക്കാം എന്നതാണ് പോരായ്മ. സ്നാപ്പ് ഹുക്ക് കണക്ഷൻ തിരിച്ചറിയുന്നതിനും പൂപ്പൽ ചെലവ് വർദ്ധിപ്പിക്കുന്നതിനും സ്ലൈഡർ സംവിധാനവും ലിഫ്റ്റർ സംവിധാനവും ആവശ്യമാണ്.
2). സ്ക്രൂ സന്ധികൾ:
സ്ക്രൂ സന്ധികൾ ഉറച്ചതും വിശ്വസനീയവുമാണ്. പ്രത്യേകിച്ചും, സ്ക്രൂ + നട്ട് ഫിക്സേഷൻ വളരെ വിശ്വസനീയവും മോടിയുള്ളതുമാണ്, ഇത് വിള്ളലുകൾ ഇല്ലാതെ ഒന്നിലധികം ഡിസ്അസംബ്ലികളെ അനുവദിക്കുന്നു. വലിയ ലോക്കിംഗ് ഫോഴ്സും ഒന്നിലധികം പൊളിച്ചുനീക്കലും ഉള്ള ഉൽപ്പന്നങ്ങൾക്ക് സ്ക്രൂ കണക്ഷൻ അനുയോജ്യമാണ്. സ്ക്രൂ നിരയ്ക്ക് കൂടുതൽ സ്ഥലം എടുക്കുന്നു എന്നതാണ് പോരായ്മ.
3). മ ing ണ്ടിംഗ് മേലധികാരികൾ:
മേലധികാരികളും ദ്വാരങ്ങളും തമ്മിലുള്ള കർശനമായ ഏകോപനത്തിലൂടെ രണ്ട് ഭാഗങ്ങൾ ശരിയാക്കുക എന്നതാണ് ബോസ് കണക്ഷൻ മ ing ണ്ട് ചെയ്യുന്നത്. ഉൽപ്പന്നങ്ങൾ വിച്ഛേദിക്കാൻ അനുവദിക്കുന്ന തരത്തിൽ ഈ കണക്ഷൻ ശക്തമല്ല. ഡിസ്അസംബ്ലിംഗ് സമയം കൂടുന്നതിനനുസരിച്ച് ലോക്കിംഗ് ശക്തി കുറയും എന്നതാണ് പോരായ്മ.
4). അൾട്രാസോണിക് വെൽഡിംഗ്:
അൾട്രാസോണിക് വെൽഡിംഗ് മെഷീന്റെ പ്രവർത്തനത്തിൽ രണ്ട് ഭാഗങ്ങൾ അൾട്രാസോണിക് അച്ചിൽ ഇടുകയും കോൺടാക്റ്റ് ഉപരിതലത്തെ സംയോജിപ്പിക്കുകയും ചെയ്യുക എന്നതാണ് അൾട്രാസോണിക് വെൽഡിംഗ്. ഉൽപ്പന്ന വലുപ്പം ചെറുതായിരിക്കാം, ഇഞ്ചക്ഷൻ മോഡൽ താരതമ്യേന ലളിതമാണ്, കണക്ഷൻ ഉറച്ചതാണ്. അൾട്രാസോണിക് പൂപ്പൽ, അൾട്രാസോണിക് വെൽഡിംഗ് മെഷീൻ എന്നിവയാണ് പോരായ്മ, ഉൽപ്പന്നത്തിന്റെ വലുപ്പം വളരെ വലുതായിരിക്കരുത്. പൊളിച്ചതിനുശേഷം, അൾട്രാസോണിക് ഭാഗങ്ങൾ വീണ്ടും ഉപയോഗിക്കാൻ കഴിയില്ല.
6. അണ്ടർകട്ട്സ്
പൂപ്പലിന്റെ പകുതി നീക്കംചെയ്യുന്നതിന് തടസ്സമാകുന്ന ഇനങ്ങളാണ് അണ്ടർകട്ട്സ്. രൂപകൽപ്പനയിൽ എവിടെയും അണ്ടർകട്ടുകൾ ദൃശ്യമാകും. ഭാഗത്തെ ഡ്രാഫ്റ്റ് ആംഗിളിന്റെ അഭാവത്തേക്കാൾ മോശമല്ലെങ്കിൽ ഇവ സ്വീകാര്യമല്ല. എന്നിരുന്നാലും, ചില അടിവസ്ത്രങ്ങൾ ആവശ്യമാണ് കൂടാതെ / അല്ലെങ്കിൽ ഒഴിവാക്കാനാവില്ല. അത്തരം സന്ദർഭങ്ങളിൽ, ആവശ്യമാണ്
അച്ചിൽ ഭാഗങ്ങൾ സ്ലൈഡുചെയ്യുകയോ ചലിപ്പിക്കുകയോ ചെയ്യുന്നതിലൂടെ അണ്ടർകട്ടുകൾ നിർമ്മിക്കുന്നു.
അച്ചിൽ ഉൽപാദിപ്പിക്കുമ്പോൾ അണ്ടർകട്ടുകൾ സൃഷ്ടിക്കുന്നത് കൂടുതൽ ചെലവേറിയതാണെന്നും അത് മിനിമം സൂക്ഷിക്കേണ്ടതുണ്ടെന്നും ഓർമ്മിക്കുക.
7. പിന്തുണ റിബുകൾ / ഗുസെറ്റുകൾ
പ്ലാസ്റ്റിക് ഭാഗത്തെ വാരിയെല്ലുകൾ ഭാഗത്തിന്റെ കാഠിന്യത്തെ (ലോഡും പാർട്ട് വ്യതിചലനവും തമ്മിലുള്ള ബന്ധം) മെച്ചപ്പെടുത്തുകയും കാഠിന്യം വർദ്ധിപ്പിക്കുകയും ചെയ്യുന്നു. വാരിയെല്ലിന്റെ ദിശയിൽ ഉരുകുന്ന ഒഴുക്ക് വേഗത്തിലാക്കുന്നതിനാൽ ഇത് പൂപ്പൽ ശേഷി വർദ്ധിപ്പിക്കുന്നു.
ഭാഗത്തിന്റെ ദൃശ്യമല്ലാത്ത പ്രതലങ്ങളിൽ പരമാവധി സമ്മർദ്ദത്തിന്റെയും വ്യതിചലനത്തിന്റെയും ദിശയിൽ റിബണുകൾ സ്ഥാപിച്ചിരിക്കുന്നു. പൂപ്പൽ പൂരിപ്പിക്കൽ, ചുരുക്കൽ, പുറന്തള്ളൽ എന്നിവയും റിബൺ പ്ലെയ്സ്മെന്റ് തീരുമാനങ്ങളെ സ്വാധീനിക്കണം.
ലംബ മതിലുമായി ചേരാത്ത വാരിയെല്ലുകൾ പെട്ടെന്ന് അവസാനിക്കരുത്. നാമമാത്രമായ മതിലിലേക്ക് ക്രമേണ പരിവർത്തനം ചെയ്യുന്നത് സമ്മർദ്ദ കേന്ദ്രീകരണത്തിനുള്ള സാധ്യത കുറയ്ക്കും.
റിബൺ - അളവുകൾ
വാരിയെല്ലുകൾക്ക് ഇനിപ്പറയുന്ന അളവുകൾ ഉണ്ടായിരിക്കണം.
സിങ്ക് മാർക്ക് ഒഴിവാക്കാൻ റിബൺ കനം നാമമാത്രമായ മതിൽ കനം 0.5 മുതൽ 0.6 മടങ്ങ് വരെ ആയിരിക്കണം.
വാരിയെല്ലിന്റെ ഉയരം നാമമാത്രമായ മതിൽ കനം 2.5 മുതൽ 3 മടങ്ങ് വരെ ആയിരിക്കണം.
പുറന്തള്ളൽ സുഗമമാക്കുന്നതിന് റിബണിന് 0.5 മുതൽ 1.5 ഡിഗ്രി ഡ്രാഫ്റ്റ് ആംഗിൾ ഉണ്ടായിരിക്കണം.
റിബൺ ബേസിന് 0.25 മുതൽ 0.4 മടങ്ങ് വരെ മതിൽ കനം ഉണ്ടായിരിക്കണം.
രണ്ട് വാരിയെല്ലുകൾ തമ്മിലുള്ള ദൂരം 2 മുതൽ 3 മടങ്ങ് (അല്ലെങ്കിൽ കൂടുതൽ) നാമമാത്ര മതിൽ കനം ആയിരിക്കണം.
8. റേഡിയസ്ഡ് അരികുകൾ
രണ്ട് ഉപരിതലങ്ങൾ കണ്ടുമുട്ടുമ്പോൾ, അത് ഒരു മൂലയായി മാറുന്നു. മൂലയിൽ, മതിൽ കനം നാമമാത്രമായ മതിൽ കനം 1.4 മടങ്ങ് വർദ്ധിക്കുന്നു. ഇത് ഡിഫറൻഷ്യൽ ചുരുങ്ങലിനും വാർത്തെടുത്ത സമ്മർദ്ദത്തിനും കൂടുതൽ തണുപ്പിക്കൽ സമയത്തിനും കാരണമാകുന്നു. അതിനാൽ, സേവനത്തിൽ പരാജയപ്പെടാനുള്ള സാധ്യത മൂർച്ചയുള്ള കോണുകളിൽ വർദ്ധിക്കുന്നു.
ഈ പ്രശ്നം പരിഹരിക്കുന്നതിന്, കോണുകൾ ആരം ഉപയോഗിച്ച് മൃദുവാക്കണം. ദൂരം ബാഹ്യമായും ആന്തരികമായും നൽകണം. ആന്തരിക മൂർച്ചയുള്ള കോണിൽ ഒരിക്കലും വിള്ളൽ പ്രോത്സാഹിപ്പിക്കുന്നില്ല. മതിൽ കനം സ്ഥിരമായി സ്ഥിരീകരിക്കുന്ന തരത്തിലായിരിക്കണം ദൂരം. കോണുകളിൽ മതിൽ കനം 0.6 മുതൽ 0.75 മടങ്ങ് വരെ ദൂരമുള്ളതാണ് നല്ലത്. ആന്തരിക മൂർച്ചയുള്ള കോണിൽ ഒരിക്കലും വിള്ളൽ പ്രോത്സാഹിപ്പിക്കുന്നില്ല.
9.സ്ക്രൂ ബോസ് ഡിസൈൻ
രണ്ട് പകുതി കേസുകൾ ഒരുമിച്ച് പരിഹരിക്കുന്നതിന് ഞങ്ങൾ എല്ലായ്പ്പോഴും സ്ക്രൂകൾ ഉപയോഗിക്കുന്നു, അല്ലെങ്കിൽ പിസിബിഎ അല്ലെങ്കിൽ മറ്റ് ഘടകങ്ങൾ പ്ലാസ്റ്റിക് ഭാഗങ്ങളിൽ ഉറപ്പിക്കുക. അതിനാൽ സ്ക്രൂ ബോസുകളാണ് സ്ക്രൂ ചെയ്യുന്നതിനും നിശ്ചിത ഭാഗങ്ങൾക്കുമുള്ള ഘടന.
സ്ക്രൂ ബോസ് സിലിണ്ടർ ആകൃതിയിലാണ്. ബോസിനെ അമ്മയുടെ ഭാഗവുമായി ബന്ധിപ്പിക്കാം അല്ലെങ്കിൽ അത് വശത്ത് ബന്ധിപ്പിക്കാം. വശത്ത് ലിങ്കുചെയ്യുന്നത് പ്ലാസ്റ്റിക്ക് കട്ടിയുള്ള ഭാഗത്തിന് കാരണമായേക്കാം, ഇത് അഭികാമ്യമല്ല, കാരണം ഇത് സിങ്ക് മാർക്കിന് കാരണമാവുകയും തണുപ്പിക്കൽ സമയം വർദ്ധിപ്പിക്കുകയും ചെയ്യും. സ്കെച്ചിൽ കാണിച്ചിരിക്കുന്നതുപോലെ ബോസിനെ ഒരു വാരിയെല്ലിലൂടെ വശത്തെ മതിലുമായി ബന്ധിപ്പിക്കുന്നതിലൂടെ ഈ പ്രശ്നം പരിഹരിക്കാനാകും. നിതംബ വാരിയെല്ലുകൾ നൽകി ബോസിനെ കർക്കശമാക്കാം.
മറ്റേതെങ്കിലും ഭാഗം ഉറപ്പിക്കാൻ ബോസിൽ സ്ക്രീൻ ഉപയോഗിക്കുന്നു. ത്രെഡ് രൂപപ്പെടുത്തുന്ന തരത്തിലുള്ള സ്ക്രൂകളും ട്രെഡ് കട്ടിംഗ് തരം സ്ക്രൂകളും ഉണ്ട്. ത്രെഡ് രൂപപ്പെടുത്തുന്ന സ്ക്രൂകൾ തെർമോപ്ലാസ്റ്റിക്സിലും ത്രെഡ് കട്ടിംഗ് സ്ക്രൂകൾ അനലസ്റ്റിക് തെർമോസെറ്റ് പ്ലാസ്റ്റിക് ഭാഗങ്ങളിലും ഉപയോഗിക്കുന്നു.
ത്രെഡ് രൂപപ്പെടുത്തുന്ന സ്ക്രൂകൾ ബോസിന്റെ ആന്തരിക ഭിത്തിയിൽ തണുത്ത പ്രവാഹം വഴി പെൺ ത്രെഡുകൾ ഉൽപാദിപ്പിക്കുന്നു - മുറിക്കുന്നതിനേക്കാൾ പ്ലാസ്റ്റിക്ക് പ്രാദേശികമായി രൂപഭേദം വരുത്തുന്നു.
സ്ക്രൂ ഉൾപ്പെടുത്തൽ ശക്തികളെയും സേവനത്തിലെ സ്ക്രൂവിൽ സ്ഥാപിച്ചിരിക്കുന്ന ലോഡിനെയും നേരിടാൻ സ്ക്രൂ ബോസ് ശരിയായ അളവുകൾ ഉണ്ടായിരിക്കണം.
ത്രെഡ് സ്ട്രിപ്പിംഗിനും സ്ക്രൂ പുറത്തെടുക്കുന്നതിനുമുള്ള പ്രതിരോധത്തിന് സ്ക്രൂവുമായി ബന്ധപ്പെട്ട ബോറിന്റെ വലുപ്പം നിർണ്ണായകമാണ്.
ത്രെഡ് രൂപപ്പെടുന്നതിലൂടെ വളയുന്ന സമ്മർദ്ദങ്ങളെ നേരിടാൻ ബോസിന്റെ പുറം വ്യാസം വലുതായിരിക്കണം.
ഒരു ചെറിയ നീളത്തിൽ പ്രവേശന ഇടവേളയിൽ ബോറിന് അല്പം വലിയ വ്യാസമുണ്ട്. വാഹനമോടിക്കുന്നതിനുമുമ്പ് സ്ക്രൂ കണ്ടെത്തുന്നതിന് ഇത് സഹായിക്കുന്നു. ഇത് ബോസിന്റെ തുറന്ന അറ്റത്ത് സമ്മർദ്ദം കുറയ്ക്കുന്നു.
പോളിമർ നിർമ്മാതാക്കൾ അവരുടെ മെറ്റീരിയലുകൾക്കായി ബോസിന്റെ അളവ് നിർണ്ണയിക്കുന്നതിനുള്ള മാർഗ്ഗനിർദ്ദേശങ്ങൾ നൽകുന്നു. സ്ക്രൂ നിർമ്മാതാക്കൾ സ്ക്രൂവിന്റെ ശരിയായ ബോറിന്റെ വലുപ്പത്തിനുള്ള മാർഗ്ഗനിർദ്ദേശങ്ങളും നൽകുന്നു.
ബോസിലെ സ്ക്രൂ ബോറിനുചുറ്റും ശക്തമായ വെൽഡ് സന്ധികൾ ഉറപ്പാക്കാൻ ശ്രദ്ധിക്കണം.
ആക്രമണാത്മക അന്തരീക്ഷത്തിൽ പരാജയപ്പെടാൻ സാധ്യതയുള്ളതിനാൽ ബോസിൽ ഉണ്ടാകുന്ന സമ്മർദ്ദം ഒഴിവാക്കാൻ ശ്രദ്ധിക്കണം.
ബോസിലെ ബോര് ത്രെഡ് ഡെപ്തിനേക്കാൾ ആഴത്തിലായിരിക്കണം.
10. ഉപരിതല അലങ്കാരം
ചിലപ്പോൾ, നല്ല രൂപം ലഭിക്കുന്നതിന്, പ്ലാസ്റ്റിക് കേസിന്റെ ഉപരിതലത്തിൽ ഞങ്ങൾ പലപ്പോഴും പ്രത്യേക ചികിത്സ നടത്തുന്നു.
ടെക്സ്ചർ, ഉയർന്ന ഗ്ലോസി, സ്പ്രേ പെയിന്റിംഗ്, ലേസർ കൊത്തുപണി, ഹോട്ട് സ്റ്റാമ്പിംഗ്, ഇലക്ട്രോപ്ലേറ്റിംഗ് തുടങ്ങിയവ. ഉൽപ്പന്നത്തിന്റെ രൂപകൽപ്പനയിൽ മുൻകൂട്ടി കണക്കിലെടുക്കേണ്ടത് ആവശ്യമാണ്, തുടർന്നുള്ള പ്രോസസ്സിംഗ് നേടാൻ കഴിയില്ല അല്ലെങ്കിൽ ഉൽപ്പന്ന അസംബ്ലിയെ ബാധിക്കുന്ന വലുപ്പ മാറ്റങ്ങൾ.